What problems should be paid attention to in the PCB circuit board stack-up design? Below is the advice given by our professional engineers with extensive PCB design experience.
When designing a stack up, be sure to follow two rules:
- Each trace layer must have an adjacent reference layer (power or ground);
- The adjacent main power plane and the ground plane should maintain a minimum distance to provide larger coupling capacitance.
Let’s take an example of two, four, and six-layer PCB boards to illustrate:
Lamination of single-sided and double-sided PCBs
For a double-layer CB board, controlling EMI radiation is mainly considered from the routing and layout.
The electromagnetic compatibility problem of single-layer PCB boards and double-layer PCB boards is becoming more and more prominent. The main reason for this phenomenon is that the signal loop area is too large, which produces intense electromagnetic radiation and makes the circuit sensitive to external interference. To improve the electromagnetic compatibility of the line, the easiest way is to reduce the loop area of the key signal; the key signal mainly refers to the signal that produces intense radiation and the signal that is sensitive to the outside world.
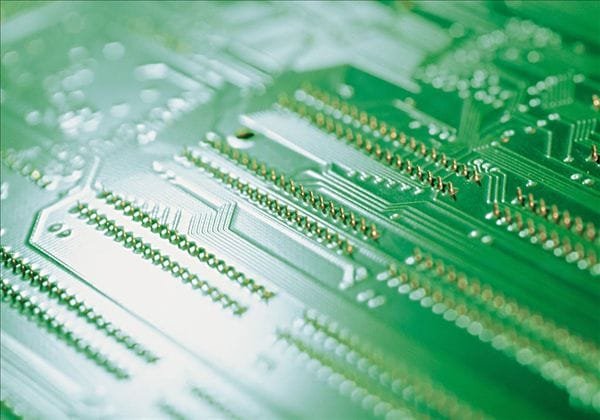
Single and double layer circuit boards are usually used in low-frequency analog designs below 10KHz
1) The power circuit on the same layer are routed radially, and the sum of the lengths of the circuit is minimized;
2) When laying out the power supply and ground circuit, they should be close to each other; lay a ground routing on the side of the critical signal, and this ground routing should be as close to the signal routing as possible. In this way, a smaller loop area is formed, and the sensitivity of differential mode radiation to external interference is reduced.
3) If it is a double-layer circuit board, you can lay a ground routing along with the signal routing on the other side of the circuit board, close to the bottom of the signal routing, and the circuit should be as wide as possible.
Lamination of four-layer PCB boards
- SIG-GND(PWR)-PWR (GND)-SIG,
- GND-SIG(PWR)-SIG(PWR)-GND,
The potential problem for the above two stack-up designs is for the traditional 1.6mm (62mil) board thickness. The layer spacing will become very large, which is not conducive to controlling impedance, interlayer coupling, and shielding; significantly, the large spacing between the power supply layer and the ground layer reduces the board capacitance and is not conducive to filtering noise.
The first solution is usually used when there are many chips on the PCB board. This scheme can get better SI performance, but not very good for EMI performance, mainly controlled by traces and other details.
The second solution is usually used when the chip density on the PCB is low enough, and there is enough space around the chip. In this scheme, the outer layers of the PCB are ground layers, and the two middle layers are signal/power layers. This is the best 4-layer PCB structure available from an EMI control perspective.
Note: The distance between the middle two signal and power mixed layers should be widened. The wiring direction should be vertical to avoid crosstalk; the board area should be adequately controlled to reflect the 20H rule.
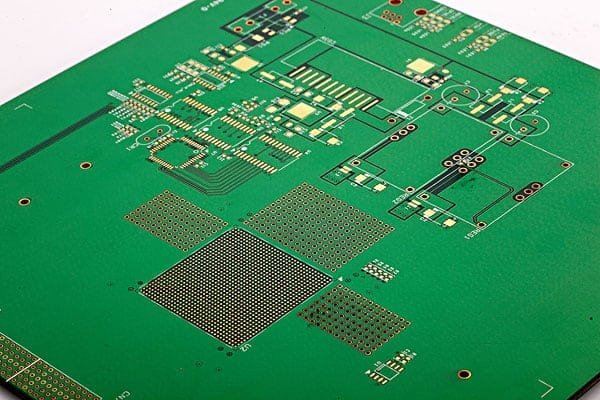
Lamination of six-layer PCB board
For the design with high chip density and high clock frequency, the design of a 6-layer PCB board should be considered. The recommended stacking method is as follows:
- SIG-GND-SIG-PWR-GND-SIG;
This stack-up scheme results in better signal integrity. The signal layer is adjacent to the ground layer, the power layer and the ground layer are paired, the impedance of each trace layer can be well controlled, and both ground layers can absorb magnetic lines of force well.
- GND-SIG-GND-PWR-SIG-GND;
This solution is only suitable for the case where the density of components is not very high. This kind of stack has all the advantages of the above stack, and the ground planes of the top and bottom layers are relatively complete, which can be used as a better shielding layer. Therefore, the EMI performance is better than the first solution.
Summary: Comparing the first scheme with the second scheme, the cost of the second scheme is significantly increased. Therefore, we usually choose the first solution when stacking.
Recommended Posts
Choosing the right PCB manufacturer and supplier. An ultimate quest that will payback in the future.
When we start a new product project, choosing a suitable PCB manufacturer and supplier is the first step and an essential step in the success of our project.
What is the Bill of Materials(BOM) and how to create one?
Bill of Materials (BOM) is an important file that contains comprehensive information on the components/parts required in the PCB. The buyer creates a BOM file of the PCB and provides it to the manufacturer/assembler.
Exploring the Benefits and Challenges of China PCB Prototype Manufacturing
In this blog post, we will explore the benefits and challenges of China PCB prototype manufacturing and share some insights on how to find a reliable PCB prototype manufacturer.
How To Testing A PCB For Short Circuit?
The quality control methods of printed circuit boards mainly include testing and inspection. PCB testing and inspection methods include Visual inspection, Multimeter testing, Destructive testing, etc.
PCB Prototype Cost: An In-Depth Look at What Determines the Price
Prototyping is an essential step in the development process of any electronic product. Creating a PCB prototype allows you to physically validate and test your circuit design, identify potential flaws, and gather valuable feedback before committing to full-scale production. However, the cost of PCB prototyping can vary significantly depending on factors such as board size, layer count, materials, finishes, production quantity, and special requirements. In this comprehensive guide, we explore these key cost determinants in depth and provide cost-saving tips to help you optimize your PCB prototype expenses without compromising quality or functionality.
The Importance of Choosing a Reliable PCB Prototype Manufacturer
At JHYPCB, we are a specialized PCB prototype manufacturer, and in this article, we will discuss the importance of choosing a reliable PCB prototype manufacturer.